Hot Wire CNC Foam Cutter – Precision Cutting
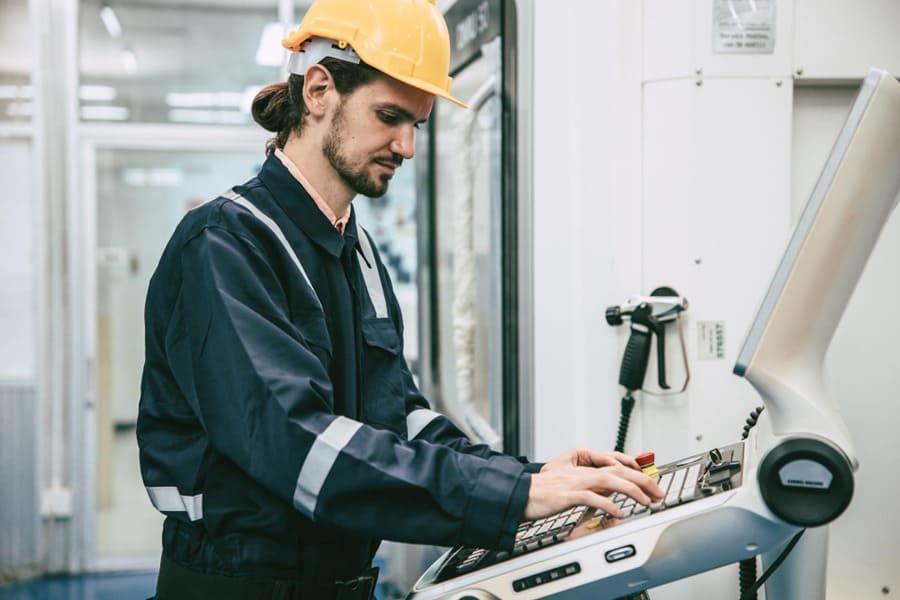
Welcome to the cutting-edge realm of the hot wire CNC foam cutter, where precision foam cutting merges with modern technology to redefine the standards of craft and design. If you’ve ever dreamed of bringing your intricate design ideas to life, the precision and control offered by these dynamic tools might just be your gateway to excellence.
At the heart of this technology lies the CNC – Computer Numerical Control – which transforms your digital designs into reality. Imagine cutting through foam with the kind of accuracy that leaves every edge smooth and every curve as intended, without the laborious effort of manual cutting. Whether it’s for your personal projects or professional designs, these state-of-the-art machines are crafted to enhance the quality and appearance of your work effortlessly.
Join us as we delve into the sophistication of cutting-edge foam cutters and discover how the precision and efficiency of a hot wire CNC machine can elevate your projects beyond your expectations.
Understanding the Basics of Hot Wire CNC Technology
Embarking on the journey of foam crafting and design, you’ve likely come across the term hot wire CNC. This innovative CNC technology is transforming the way we approach foam cutting technology. But what exactly is it and how does it work? You can take a look at example images of machines with this technology at https://www.megaplot.com/hot-wire-cnc-foam-cutter/ essentially, it involves a heated wire that easily slices through material such as expanded polystyrene (EPS). This technology allows achieving cuts with a level of precision that manual techniques simply cannot match.
At the heart of this process is the hot wire cnc machine, which integrates advanced software to direct the wire’s path with exacting accuracy. This level of control facilitates not just simple cuts, but also allows for the creation of complex shapes and designs that were once unthinkable outside of high-end manufacturing processes. You may find it surprising how this sophisticated technique boils down to the finely tuned movement of a wire, guided by the meticulous commands of a computer program.
- Pre-programmed patterns ensure that each cut is consistent, eliminating the variable nature of manual cutting.
- Speed is significantly enhanced, empowering users to complete projects in a fraction of the time it once took.
- The wire’s temperature is precisely regulated to make clean cuts that help minimize additional finishing work.
The evolution of CNC technology means that hot wire foam cutters are now more accessible than ever, allowing a broad spectrum of industries to harness the benefits of this technology. From intricate architectural models and theater set designs to custom packaging solutions, the impact is widespread and growing. The consistent quality, allied with the speed of delivery that hot wire CNC machines offer, places them firmly at the forefront of foam cutting options available today.
Essential Components of a Hot Wire CNC Foam Cutter
As you delve into the realm of foam crafting and production, understanding the key components of a hot wire foam cutter is crucial for achieving precise and efficient results. Let’s dissect the vital parts that play a role in the machine’s functionality.
- Cutting Wire:The heart of a hot wire foam cutter, this specialized wire heats up to effortlessly slice through foam. Its quality affects precision and the smoothness of the cut.
- Power Supply:A consistent power source is essential, providing the necessary electricity to heat the wire to the correct temperature for cutting different types of foam.
- Wire Tensioning System:Proper tension is key to maintaining consistent cuts and preventing wire sag. A well-designed system will offer easy adjustments for various project requirements.
- Cutting Bed:This platform supports the foam during the cutting process. Look for a cutting bed that’s flat, sturdy, and expansive enough to accommodate your foam sheets.
- CNC Controller:The brains of the operation, this component translates your designs into precise movements of the cutting wire through CNC foam cutting elements.
- Software:It’s the interface where you’ll design or upload your foam cutting patterns. User-friendly software can significantly streamline your workflow.
Each of these foam cutter components works in unison to ensure that your cuts are accurate and your final product meets expectations. When assessing various machines, consider the quality and engineering of these elements to make an informed decision that suits your creative or commercial needs. Remember, in the world of CNC cutting, precision and reliability are paramount to success.
Step-by-Step Process: How to Use a Hot Wire CNC Foam Cutter
Embarking on a new project with your hot wire CNC machine can be both exciting and daunting. However, with a clear understanding of the foam cutting process and a handy CNC cutting guide, you can approach this task with confidence. Using a hot wire CNC machine is not as complex as it might seem, and by following these steps, you’ll be well on your way to crafting precise, intricate foam creations.
- Designing Your Foam Object: Begin by creating a design for your foam object using compatible CAD software. Ensure that your design is precise, as the hot wire CNC machine will replicate it exactly.
- Software Setup: Once your design is ready, transfer it to the CNC machine’s software system. This step will typically involve setting parameters such as cutting speed and wire temperature to match the type of foam you’ll be cutting.
- Material Placement: Securely place your foam block onto the cutting bed of the machine. Make sure it’s stable to avoid any movement during cutting, which could affect the precision of your cut.
- Begin the Cutting Process: With everything in place, start the cutting process. Monitor the operation to ensure it runs smoothly. Hot wire CNC machines are known for their precision, so you should expect an accurate reproduction of your design.
- Safety First: Bear in mind all safety practices when using the machine. Always wear protective gear, keep your hands clear from the wire when in operation, and understand the emergency stop functions.
By following these steps, using hot wire CNC machine technology becomes a straightforward and highly effective way to handle your foam cutting projects. Whether you’re a beginner or a seasoned professional, the process rewards you with precise cuts and incredible detail that manual methods can’t match. Keep this CNC cutting guide handy, and you’ll find the foam cutting process to become a seamless part of your workflow.
Hot Wire CNC Foam Cutter: Precision Profiles and Designs
Imagine effortlessly creating complex profiles and stylish designs out of foam with a precision that seems almost unreal. That’s the power of precision foam cutting with a hot wire CNC foam cutter – it’s like wielding the brush of an artist with the exactitude of an engineer. Achieving intricate foam designs that were once considered challenging, or even impossible, with conventional cutting methods is now within your grasp.
The distinctive aspect of using a hot wire CNC foam cutter lies in its capability to carry out clean cuts that dramatically reduce the need for additional finishing work like sanding. Less post-processing not only saves you time, but it also preserves the pristine quality of your unique designs. Let’s delve into how these innovative machines enhance your creative journey through the world of foam crafting and design.
- Discover how the cutter’s specialized hot wire CNC profiles allow you to execute fine, detailed cuts without the mess of rough edges.
- Learn about the boon of minimal dust and debris, courtesy of the hot wire’s ability to seal edges as it slices through the foam.
- Explore a variety of projects, from bespoke packaging inserts to delicate architectural models, benefitting from this technology.
- Realize the broadly expanded artistic possibilities, as the cutter’s versatility supports complex design executions that go beyond straight cuts and basic shapes.
Whether you’re a professional looking to refine your craft or a hobbyist eager to push the boundaries of your creations, the hot wire CNC foam cutter stands as an indispensable tool. It’s the gateway to not only perfecting current projects but also unlocking an entirely new realm of possibilities in precision foam cutting.
The Wide Range of Applications for Hot Wire Foam Cutting
Hot wire foam cutting is not just a technique; it’s a revolution across diverse sectors. With foam cutting applications being nearly as vast as your imagination, hot wire CNC versatility has become the go-to solution for professionals and hobbyists alike. From creating detailed architectural models that give a realistic perspective to future constructions to sculpting magical sets that transport theater audiences to other worlds, the versatile hot wire cutter is changing the way we approach design and manufacturing.
- Architectural Modeling: Architects rely on precision to bring their blueprints to life. With hot wire CNC foam cutters, crafting scale models with immaculate accuracy has become more practical, making it easier to visualize and refine designs before they are built on actual scale.
- Theatrical Set Design: In the world of theater, where the sets can be as important as the actors themselves, these cutters allow designers to create elaborate and intricate backdrops quickly, making productions more dynamic and visually captivating for the audience.
In specialized packaging solutions, where protecting valuable goods is paramount, custom foam inserts are precisely carved out for items of any shape or size. Similarly, the aeronautics industry benefits significantly; components with strict tolerances and lightweight but strong structures are needed, and hot wire CNC foam cutting meets these rigorous demands seamlessly.
- Educational Environments: In classrooms and workshops, students can take their engineering and art projects to new heights, merging creativity with technological prowess to make theoretical concepts tangible.
- Hobbyist Projects: For hobbyists, creating models, custom vehicle parts, and intricate art pieces are now within reach, thanks to the affordable and versatile hot wire cutters that transform a simple block of foam into a masterpiece.
The versatility of hot wire CNC machines is a game-changer in many other fields too. You might be amazed at how they’re shaping the way we create, package, and educate. As you embrace these tools, you empower yourself to turn your visionary ideas into precise, tangible realities.
Maintaining Your Hot Wire CNC Foam Cutter for Longevity
Meticulous upkeep is paramount for ensuring that your hot wire CNC foam cutter stands the test of time. Engaging in regular foam cutter maintenance not only fortifies the longevity of your equipment but also ensures consistent quality in your cuts. Below, we dive into the essential maintenance practices that will keep your device in prime condition.
- Clean the equipment after each use to prevent the accumulation of foam residue, which can affect the machine’s functionality over time.
- Inspect the wire tension routinely since proper tension is crucial for precision cutting. A slack wire may result in inaccurate cuts or wire breakage.
- Stay updated with software enhancements as they can improve the efficiency of your foam cutter and introduce new capabilities or bug fixes.
Tackling common issues promptly can prevent further complications, safeguarding your investment. Learning to spot signs of wear, such as erratic cutting or unusual machine noises, lets you address them before they escalate. Remember, prolonging cutter lifespan is not just about reactive measures but also proactively maintaining its condition. Implement these practices, and your hot wire CNC upkeep efforts will pay off, granting you countless hours of uninterrupted, precise foam cutting.
Tips and Tricks to Optimize Your Foam Cutting Projects
Embarking on a project that involves foam can be an exciting venture whether you’re a professional or a hobbyist looking to hone your craft. To truly optimize foam cutting and ensure your results are anything but subpar, consider integrating a few key strategies that revolve around precision foam cutting techniques and hot wire precision. By focusing on these aspects, you’ll not only achieve cleaner cuts but also elevate the quality of your final product.
- Achieving Smoother Edges: One of your primary goals should be to ensure that your foam cuts are as smooth as possible. This often involves maintaining proper wire tension and temperature, granting you clean, melt-free edges. Additionally, you might want to explore multiple passes with reduced speed, especially for thicker foam blocks, to maintain hot wire precision without overworking the material.
- Perfect Angles and Consistent Cuts: Consistency is key in foam cutting. Utilize templates and jigs wherever possible to replicate perfect angles and uniform shapes. This not only expedites your cutting process but also reduces human error, ensuring each cut is consistent with the last.
- Leveraging Software for Design Complexity: Your hot wire CNC foam cutter is equipped with software that can handle intricate designs with ease. Don’t shy away from harnessing this technology to experiment with complex patterns and shapes that might have seemed daunting before. By using the software to its full capability, you can transform a simple idea into a work of art.
Optimizing your projects goes beyond the cutting phase. Consider the entire lifecycle of your materials for a truly efficient approach:
- Minimizing Foam Waste: Plan your projects in a way that maximizes the use of your foam. Nest your designs during the planning stage to utilize as much of the material as possible, reducing waste and cost.
- Enhancing Productivity: Refine your workflow by organizing your workspace and preparing your designs in advance. This way, when it’s time to cut, you can operate seamlessly without unnecessary interruptions.
- Repurposing Excess Material: Gain a creative edge by thinking of ways to repurpose any excess foam. Small pieces can be turned into detailed accents for larger projects, or even used for practice runs without utilizing fresh material.
Keep these tips in mind, and you’ll find that with each foam cutting project, your skills will significantly improve. By optimizing your approach and embracing these techniques, you’ll elevate your creations from mere concepts to exceptional realities.
Comparing Hot Wire CNC Foam Cutters to Traditional Cutting Methods
When stepping into the realm of foam cutting, you quickly encounter two distinct paths: the traditional approach with manual tools and the advanced journey using hot wire CNC foam cutters. More than a simple choice of technique, this decision can significantly impact your craftsmanship and productivity.
Traditional vs CNC Foam Cutting: The conventional methods, though straightforward, often struggle to maintain consistency and precision, particularly for large or intricate designs. Manual cuts demand a high level of skill and physical labor, which may not always yield the meticulous detail or reproducibility that CNC foam cutting can guarantee. Hot wire CNC technology outshines traditional tools by precisely carving foam according to digital designs fed into a computer, offering you unmatched precision on every cut.
- Automated precision ensures that your designs are replicated exactly as intended, without discrepancies.
- Speed is on your side with CNC foam cutting, making quick work of projects that would otherwise take hours by hand.
- CNC cutting advantages include reduced labor as the machine performs the cuts while you focus on design and other tasks.
- The ability to scale up production is a palpable benefit when using CNC foam cutters, allowing you to fulfill larger orders that would be impractical with manual methods.
Hot wire cutting benefits don’t stop at efficiency and precision – it also propels your projects to new heights by enabling complex cuts that defy traditional hand-cutting methods. Diving into the world of CNC foam cutting, your creativity is no longer bound by the limitations of your tools.
- Evaluate the scope and scale of your projects to determine the appropriateness of CNC foam cutting.
- Consider the long-term savings in time and materials that can result from improved accuracy.
- Think about the added value of being able to execute complex, intricate designs that could expand your market opportunities.
Faced with the global trend towards automation, CNC foam cutting technology is reshaping industry standards. Where once traditional methods were the benchmark, CNC’s superior capabilities are now the new norm, heralding a significant leap forward in production quality and efficiency.
Investing in a Hot Wire CNC Foam Cutter: What to Consider
When you’re looking to enhance your fabrication capabilities, investing in a hot wire CNC foam cutter can be a transformative decision. Whether for business expansion or personal creative projects, it’s crucial to gauge a few key considerations that can significantly influence the success of your investment. To begin with, the size of the machine is paramount; it must accommodate the scale of the projects you intend to undertake. After all, the right balance between workspace footprint and operational capacity can dictate productivity and efficiency.
Compatibility with diverse foam materials also stands out as a vital criterion. Your foam cutter investment should not be hindered by material restrictions but rather support a broad range of foam types to maximize versatility and usage scenarios. Precision requirements are equally essential, especially when your work relies on the cutter’s ability to deliver exact cuts that mirror your designs flawlessly. Furthermore, be mindful of budget constraints, but also consider how this investment aligns with your long-term goals. Choosing a foam cutter that adapts to your evolving needs can future-proof your purchase, preventing the need for costly upgrades or replacements down the line.
Lastly, the practical aspects of ownership such as customer service, comprehensive warranty, and the availability of replacement parts can’t be overstated. These factors are not mere afterthoughts but core components of the value derived from investing in hot wire CNC technology. They ensure that your equipment remains a reliable asset, capable of consistent operation and performance. As you deliberate on which hot wire CNC foam cutter to acquire, prioritize these points to ensure that the choice you make empowers you to bring your projects to life with precision, efficiency, and satisfaction.